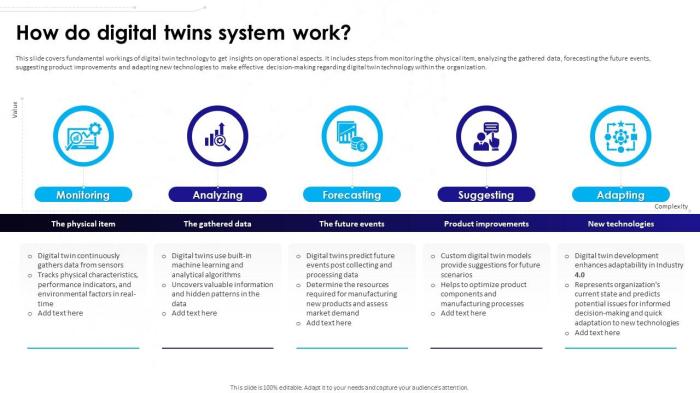
How digital twins are unlocking remote work for blue collar workers? This innovative approach is revolutionizing the way tradespeople work, offering new possibilities for remote collaboration, training, and efficiency. Imagine a plumber fixing a leak in a remote location, guided by a virtual replica of the house’s plumbing system. This is the power of digital twins, creating a virtual space that mirrors the real world, empowering blue-collar workers to perform their jobs efficiently and safely from afar.
From construction sites to manufacturing plants, digital twins are already proving their value. These virtual models allow for real-time monitoring and control of equipment and processes, enabling remote workers to access crucial data and insights. This technology streamlines operations, optimizes performance, and opens doors to new levels of efficiency, all while fostering a more flexible and adaptable work environment for blue-collar professionals.
Introduction to Digital Twins in Remote Work: How Digital Twins Are Unlocking Remote Work For Blue Collar Workers
Digital twins are virtual representations of physical assets, processes, or systems. They’re increasingly important in various industries, allowing for simulation, analysis, and optimization in real-world scenarios. From manufacturing plants to healthcare facilities, digital twins are proving invaluable for remote monitoring and control. In blue-collar work, digital twins can revolutionize how technicians and workers operate, diagnose issues, and complete tasks remotely, enhancing efficiency and safety.Digital twins leverage data from sensors and other sources to create detailed, dynamic models of the real-world counterparts.
These models can be used to simulate different scenarios, predict potential problems, and test new solutions before implementing them in the physical environment. This simulation capability is especially crucial for blue-collar work, where complex machinery and processes need careful consideration.
Digital Twins in Blue-Collar Work
Digital twins offer numerous benefits for remote workers in blue-collar fields. They provide a platform for real-time monitoring of equipment and processes, allowing workers to identify potential issues before they escalate. This proactive approach to maintenance and troubleshooting reduces downtime and minimizes costly repairs. Further, digital twins empower remote workers with a comprehensive understanding of the system, enabling them to make informed decisions and complete tasks more effectively.
Simulation of Real-World Environments
Digital twins simulate real-world environments and processes by incorporating data from various sources, such as sensors, historical records, and expert knowledge. This data-driven approach allows for the creation of highly detailed and accurate models. These models are then used to simulate different operational conditions, allowing for experimentation and optimization without impacting the actual physical system. For example, a digital twin of a construction site can simulate the effects of different weather patterns on equipment performance or material handling, providing valuable insights for remote planning and management.
Digital twins are revolutionizing remote work for blue-collar workers, allowing them to access real-time data and instructions from anywhere. This is particularly relevant given the growing focus on sustainability, which resonates with Pope Francis’s pope francis environment climate legacy , highlighting the importance of environmental responsibility. Ultimately, these digital tools are creating a more flexible and efficient workforce, particularly in industries like construction and manufacturing.
Benefits for Remote Workers
Digital twins offer a wide range of benefits for remote workers in blue-collar industries. These benefits include:
- Enhanced Safety: Remote monitoring of equipment and processes allows for early detection of potential hazards, enabling proactive measures to prevent accidents and ensure worker safety.
- Improved Efficiency: Digital twins can optimize workflows, minimize downtime, and streamline maintenance tasks, leading to increased efficiency and productivity for remote workers.
- Reduced Costs: Proactive maintenance and reduced downtime translate to lower repair and replacement costs, ultimately saving companies money.
- Increased Knowledge and Skill Development: Digital twins provide a platform for continuous learning and skill development for remote workers, allowing them to become more proficient in their tasks.
Industries Utilizing Digital Twins for Remote Tasks
Digital twins are already being employed in various industries for remote tasks. Examples include:
- Manufacturing: Monitoring and controlling production lines remotely, troubleshooting equipment issues, and optimizing maintenance schedules.
- Oil and Gas: Remote monitoring of pipelines and drilling rigs, predicting potential failures, and optimizing maintenance schedules.
- Construction: Simulating construction processes, managing materials, and optimizing project timelines remotely.
- Utilities: Monitoring power grids, optimizing energy distribution, and predicting and preventing outages remotely.
Comparison of Traditional Methods and Digital Twins
The following table contrasts traditional methods with digital twin approaches for remote monitoring and control:
Feature | Traditional Methods | Digital Twin Approach |
---|---|---|
Monitoring | Periodic inspections, manual data collection | Real-time data from sensors, automated monitoring |
Control | Manual adjustments, reactive responses | Predictive control based on simulations, automated responses |
Troubleshooting | On-site diagnosis, potentially requiring travel | Remote diagnosis using the digital twin model |
Maintenance | Reactive maintenance, potentially leading to breakdowns | Predictive maintenance based on simulations and data analysis |
Cost | Higher cost due to travel, downtime, and reactive maintenance | Lower cost due to reduced downtime and proactive maintenance |
Remote Collaboration and Communication Enhanced by Digital Twins
Digital twins, virtual representations of physical assets, are revolutionizing remote work for blue-collar professionals, particularly in sectors like manufacturing and construction. By providing real-time data and simulations, they foster enhanced collaboration and communication between remote teams and on-site personnel, improving efficiency and safety. This real-time visibility bridges the gap between remote and on-site workforces, streamlining workflows and reducing downtime.The ability to access and analyze data from a digital twin enables remote workers to participate actively in problem-solving and decision-making, regardless of their physical location.
This translates into a more agile and responsive work environment, vital in industries with dynamic project timelines and unpredictable challenges.
Real-Time Data Sharing and Collaboration
Real-time data sharing is a key advantage of digital twins in remote work environments. Data from sensors attached to equipment, processes, or the physical environment is transmitted to the digital twin, allowing remote workers to visualize the current state of the project or asset. This instantaneous access to information is critical for troubleshooting and decision-making. Shared access to the digital twin allows remote teams to collaborate effectively on solutions, fostering a sense of shared responsibility and ownership.
Improved Communication Channels and Tools
Digital twins facilitate a variety of communication channels, streamlining interactions between remote and on-site personnel. Dedicated communication platforms integrated with the digital twin can alert remote workers to critical issues, such as equipment malfunctions or safety hazards. This proactive approach minimizes delays and potential safety risks. The use of chat functionalities allows for real-time discussions and quick responses to urgent queries.
Seamless Information Exchange
The seamless information exchange facilitated by digital twins between remote workers and on-site supervisors is crucial. Supervisors can monitor the progress of tasks, provide real-time guidance, and address any challenges encountered by remote teams using the digital twin’s visualization capabilities. This transparency enhances trust and improves communication flow. Instantaneous feedback loops between remote teams and supervisors are key to effective problem-solving.
Digital twins are revolutionizing remote work for blue-collar workers, allowing them to access and manipulate complex systems from afar. This is incredibly valuable, especially when considering the recent global news surrounding the passing of Pope Francis and the varied reactions from world leaders, like the tributes and statements from JD Vance and Donald Trump, as detailed in this article here.
While the world grapples with such events, the continued development of these digital representations opens up exciting possibilities for remote training and maintenance, ultimately benefiting blue-collar workers worldwide.
Virtual Simulations for Training and Knowledge Transfer
Virtual simulations using digital twins offer an effective method for training and knowledge transfer in remote work environments. Remote workers can practice complex procedures, troubleshoot issues, and receive real-time feedback within the simulated environment, reducing the need for physical training sessions. This approach allows for continuous learning and skill development, especially beneficial for complex machinery operation or maintenance tasks.
By simulating various scenarios, digital twins enable remote teams to develop proficiency and address potential issues in a controlled environment.
Comparison of Communication Tools
Communication Tool | Description | Digital Twin Integration | Advantages in Remote Work |
---|---|---|---|
Instant Messaging (e.g., Slack, Teams) | Real-time text-based communication | Can be integrated for notifications and quick updates from the digital twin | Quick communication, easy file sharing |
Video Conferencing (e.g., Zoom, Google Meet) | Real-time video and audio communication | Can display the digital twin during meetings for shared visualization | Visual collaboration, face-to-face interaction |
Project Management Software (e.g., Asana, Trello) | Task management and collaboration | Data from the digital twin can be integrated for task status updates | Clear task assignments, progress tracking |
Dedicated Digital Twin Platforms | Specific platforms for managing and interacting with digital twins | Core functionality | Advanced visualization, real-time data access, seamless integration with other communication tools |
Data Collection and Analysis for Improved Efficiency
Digital twins, in the context of blue-collar work, aren’t just virtual replicas; they’re powerful tools for collecting and analyzing data to optimize processes and enhance efficiency. This data-driven approach, enabled by remote monitoring, allows for continuous improvement in performance, safety, and overall productivity. Real-time insights gleaned from these digital representations are crucial for decision-making in remote work environments, fostering a more responsive and effective workforce.Data collection and analysis are at the heart of a digital twin’s effectiveness.
By gathering comprehensive data from various sources, businesses can identify trends, predict potential issues, and make informed decisions to improve operational efficiency. This allows for proactive problem-solving, reducing downtime and improving overall performance, especially crucial for remote work where direct supervision is limited.
Methods of Data Collection
Digital twins leverage a variety of methods to collect data relevant to blue-collar work. These methods include deploying sensors on equipment and tools, utilizing wearable technology for workers, and incorporating environmental monitoring systems. Each method plays a vital role in gathering comprehensive data points that are essential for the digital twin to accurately reflect the real-world scenario.
Types of Data Collected
Digital twins collect a diverse range of data, crucial for a comprehensive understanding of the work environment and individual worker performance. This includes sensor data from machinery, providing insights into operational parameters like temperature, pressure, and vibration. Machine performance metrics, like production rates and cycle times, are also collected to evaluate efficiency. Environmental factors, such as temperature, humidity, and lighting conditions, are recorded to understand the impact on worker comfort and productivity.
Data on worker movements, tools used, and safety protocols are also incorporated. This holistic approach ensures the digital twin accurately mirrors the complex interplay of factors in the workplace.
Analysis of Collected Data
The collected data is analyzed using sophisticated algorithms to identify patterns, predict potential issues, and optimize processes. This analysis often involves machine learning models that learn from historical data to identify trends and anomalies. Statistical analysis methods are also applied to understand correlations between different variables. This comprehensive analysis leads to a deeper understanding of the factors affecting productivity, worker safety, and equipment performance.
Digital twins are revolutionizing remote work for blue-collar tradespeople, allowing them to virtually interact with complex machinery and processes. While the digital world expands, it’s interesting to consider how other forms of digital communication can also be employed in this context. For example, Pope Francis’s use of social media, as seen in pope francis social media memes , shows how technology can connect with people in unexpected ways.
This highlights the potential for remote work, especially in fields like construction or manufacturing, to reach new heights through innovation and communication.
Data Analysis for Decision-Making in Remote Work
The analysis of this data is critical for remote work decision-making. For example, if sensor data indicates a machine is operating outside its optimal parameters, remote workers can be alerted and take corrective action remotely. This proactive approach avoids costly downtime and ensures continuous operation. Similarly, if environmental data suggests a worker is operating in an uncomfortable environment, adjustments can be made remotely to improve comfort and productivity.
Predictive maintenance based on historical data can also be employed to schedule maintenance proactively, further reducing downtime and improving overall efficiency.
Example of Data Analysis Supporting Decision-Making
Imagine a construction site using a digital twin. If sensor data reveals a significant increase in vibration levels on a specific piece of heavy machinery, the digital twin can alert the remote operator. This allows for immediate action to address the issue, preventing potential equipment damage and ensuring worker safety. The analysis can also identify the root cause of the issue, such as a loose bolt or worn-out part, leading to proactive maintenance scheduling.
Table: Data Types and Significance
Data Type | Description | Significance in Digital Twin |
---|---|---|
Sensor Data (Machinery) | Temperature, pressure, vibration, speed | Identify anomalies, predict equipment failures, optimize performance |
Machine Performance Metrics | Production rate, cycle time, downtime | Evaluate efficiency, identify bottlenecks, improve workflow |
Environmental Factors | Temperature, humidity, lighting, noise levels | Assess worker comfort, optimize work environment, improve safety |
Worker Data (Wearables) | Movement patterns, tool usage, safety protocols | Monitor worker safety, optimize workflows, improve productivity |
Challenges and Considerations in Implementing Digital Twins
Digital twins, while offering exciting possibilities for remote blue-collar work, aren’t without their hurdles. Successfully implementing this technology requires careful consideration of several factors, especially in a field often characterized by practical limitations and a need for tangible results. From reliable connectivity to worker training, overcoming these challenges is crucial for realizing the full potential of digital twins in this context.
Robust Internet Connectivity and Reliable Hardware
The effectiveness of digital twins hinges on continuous, high-quality data transmission. Real-time monitoring and control depend on stable internet connections. Workers in remote locations may experience intermittent connectivity, impacting the accuracy and reliability of the digital twin’s representation of the physical environment. This necessitates robust, high-bandwidth connections, potentially requiring investments in satellite internet or other solutions to ensure consistent data streams.
Furthermore, the hardware used by workers—sensors, cameras, and computing devices—must be dependable and capable of handling the data demands of a digital twin system. Downtime or malfunction of equipment can severely limit the effectiveness of the digital twin. Reliable, field-tested hardware is paramount to maintaining a continuous data stream.
Security Concerns
Remote access to physical assets through digital twins raises significant security concerns. Protecting sensitive data transmitted through the digital twin platform is crucial. Unauthorized access to equipment or data could lead to significant operational disruptions, financial losses, or even safety risks. Implementing robust security protocols, including encryption, multi-factor authentication, and access controls, is vital. Regular security audits and incident response plans are essential to mitigate potential threats and ensure the safety and integrity of the digital twin system.
Skills Gap among Blue-Collar Workers
Digital twins demand a new set of skills from blue-collar workers. Familiarity with using the digital tools, understanding the data generated, and interpreting the insights provided by the digital twin are necessary. Training programs and resources must be tailored to meet the specific needs of different blue-collar professions. Furthermore, fostering a culture of digital adoption within these communities is crucial to ensure successful integration of digital twin technology.
This requires not just technical training but also support and guidance to help workers feel comfortable and confident using these new tools.
Table Summarizing Potential Challenges and Solutions
Challenge | Potential Solution |
---|---|
Limited internet connectivity in remote locations | Implement satellite internet, use cloud-based solutions for data backup, and develop offline functionalities where possible. |
Hardware malfunctions | Use robust, field-tested equipment; Implement predictive maintenance strategies based on data from the digital twin; Have backup equipment available. |
Security vulnerabilities in remote access | Employ strong encryption protocols; Implement multi-factor authentication; Conduct regular security audits and penetration testing; Establish clear access control policies. |
Skills gap among blue-collar workers | Develop comprehensive training programs; Offer ongoing support and mentorship; Design intuitive user interfaces for the digital twin platform; Create easily accessible documentation and support resources. |
Future Trends and Implications for Blue-Collar Workers
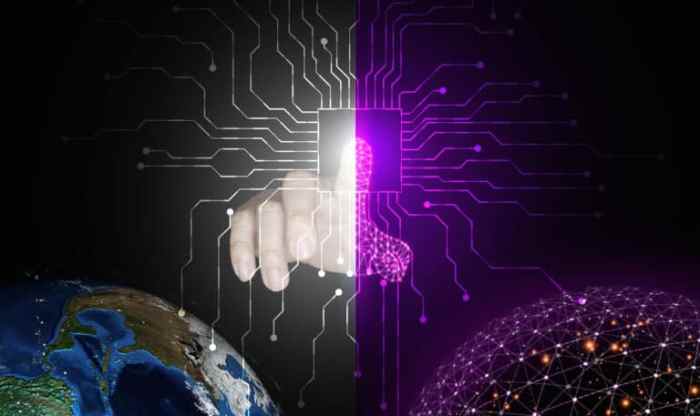
Digital twins are poised to revolutionize remote work for blue-collar professionals, offering unprecedented levels of efficiency and safety. As the technology matures, we can anticipate even more profound impacts on the future of this crucial segment of the workforce. The potential for enhanced collaboration, real-time data analysis, and automated processes is immense.The future of digital twins will not simply be an extension of current capabilities; rather, it will be a transformation driven by advancements in AI and machine learning.
This will create a symbiotic relationship between human expertise and automated systems, resulting in a more productive and safer work environment.
Potential Future Advancements in Digital Twin Technology
Digital twin technology is constantly evolving. We can expect increased integration with IoT devices, enabling more comprehensive data collection and analysis. Furthermore, advancements in 3D modeling and simulation will lead to more realistic and detailed digital representations of physical assets and processes. This will allow for more sophisticated predictive maintenance and optimization strategies. The ability to simulate various scenarios and conditions in a virtual environment will be invaluable for problem-solving and training.
Role of AI and Machine Learning in Enhancing Digital Twin Capabilities, How digital twins are unlocking remote work for blue collar workers
AI and machine learning will play a critical role in augmenting the capabilities of digital twins. Algorithms can analyze vast amounts of data collected from sensors and IoT devices, identifying patterns and anomalies that might indicate potential equipment failures or operational inefficiencies. This proactive approach to maintenance and optimization will significantly reduce downtime and improve overall productivity. Machine learning models can also personalize the digital twin experience for individual workers, adapting to their specific needs and skill sets.
Predictions for the Impact of Digital Twins on the Future of Blue-Collar Work
The impact of digital twins on blue-collar work will be substantial. Predictions include a shift towards more proactive maintenance and preventative measures, minimizing downtime and maximizing equipment lifespan. Remote collaboration will become more seamless, allowing for real-time problem-solving and knowledge sharing between geographically dispersed teams. This enhanced collaboration will contribute to improved quality control and reduced errors.
The role of human workers will evolve, focusing more on complex problem-solving, strategic decision-making, and technical expertise.
Potential for Increased Automation and Efficiency
Digital twins will enable increased automation in various aspects of blue-collar work. Tasks that are currently performed manually, such as equipment inspection or process optimization, can be automated using algorithms and robots controlled by the digital twin. This will not replace human workers but rather enhance their abilities, allowing them to focus on higher-level tasks. Predictive maintenance capabilities will significantly reduce unplanned downtime and optimize resource allocation.
Illustrative Example of a Hypothetical Future Scenario
Imagine a scenario where a construction crew is working on a skyscraper project halfway across the world. The digital twin of the building’s structural components is updated in real-time with data from sensors embedded in the materials. If an anomaly is detected, AI algorithms instantly alert the on-site team and suggest potential solutions, which can be reviewed and discussed remotely with the project manager.
The digital twin allows the team to remotely simulate various scenarios to optimize the construction process and predict potential risks before they occur, all while ensuring the safety of the workers. This example highlights the transformative potential of digital twins in enhancing safety and efficiency in remote blue-collar work.
Epilogue
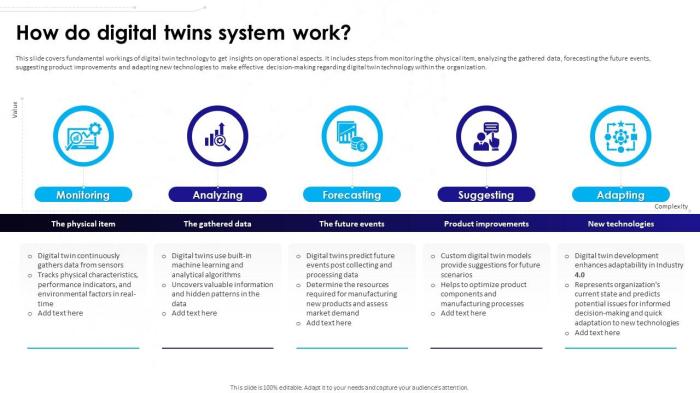
In conclusion, digital twins are poised to fundamentally reshape the blue-collar landscape. The potential for remote collaboration, enhanced training, and data-driven decision-making is immense. While challenges remain, the benefits for workers, employers, and the industry as a whole are undeniable. This transformative technology holds the key to a future where blue-collar work is more accessible, efficient, and ultimately, more rewarding for all involved.